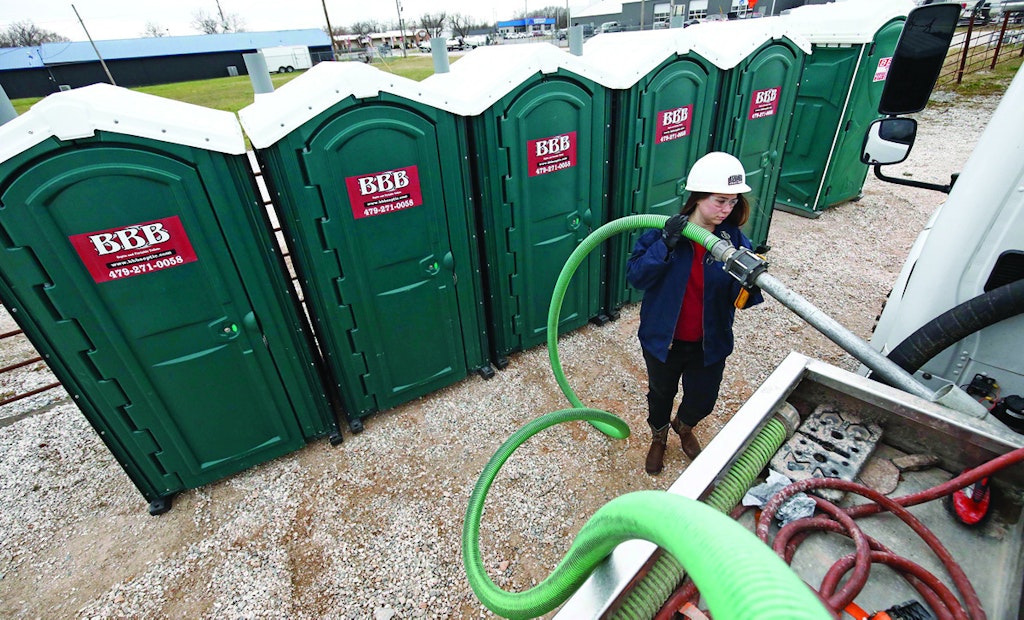
Technician Alayna Haskins returns the suction hose to the truck following a restroom service. The company’s restroom service trucks are from Best Enterprises, Longhorn Tank & Trailer and Satellite Industries.
Interested in Business & Technology ?
Get Business & Technology articles, news and videos right in your inbox! Sign up now.
Business & Technology + Get AlertsA squabbling trio of brothers bought a septic service and portable sanitation company in the early 1990s from its retiring founder and tried to hobble along with two poorly maintained vacuum trucks. It was just a matter of time before something had to change.
Finally, one of the brothers, Phil Shimer, took over and found two better-suited partners — Jon Jouvenaux and Dave Davis. Having the right team in place changed everything. The new trio proved to be a winning combination with all the required talent.
“I was a mechanic,” Jouvenaux says. “Dave was in outside sales for a lumber company so he knew a bunch of contractors. He had also gone to school to become a Wendy’s manager, so he understood accounting and payroll. And Phil and I just understood how to go to work.”
Today the company, BBB Septic and Portable Toilets in Bentonville, Arkansas, has 11 vacuum trucks and 24 employees. Jouvenaux heads marketing, business development, research and development. Davis is the general manager and oversees daily operations and financial decisions. Shimer sold out in 2015. Other management team members include operations manager Dustin Lamp and assistant general manager Taelor Ladd.
The company limits its service territory to just two counties because traveling to further sparsely populated areas doesn’t make sense economically, Jouvenaux says.
Over the years, the company added septic installations and repairs, got in on the action at Walmart’s seven-year headquarters rebuild, came up with innovative ways of hauling equipment and screening waste — and solved one of its biggest headaches, waste disposal.
EQUIPMENT LINEUP
On the portable sanitation side, the company has about 1,300 units (including 65 for events, 12 flushables, eight wheelchair-accessible, four craneable), 40 hand-wash stations, a two-unit party wagon with a drop-down deck, and 38 250-gallon holding tanks, all from Satellite Industries and PolyJohn. Their original idea of having blue units for construction and green for events got derailed during the pandemic because of supply chain issues, so they now have a full complement of colors. Hand-wash stations, which were rarely used on construction sites pre-COVID, continue to be in high demand.
Vacuum trucks include a 2017 Hino with a Best Enterprises 1,000-gallon waste/500-gallon freshwater stainless steel tank, a 2015 Freightliner M2 with a Longhorn Tank & Trailer 1,000-gallon waste/500-gallon freshwater stainless steel tank, a 2014 Dodge 5500 with a Satellite 700-gallon waste/300-gallon freshwater steel tank, and three Dodge trucks built out by Best — a 2019 5500 with a 700-gallon waste/300-gallon freshwater steel tank, a 2002 5500 with a 975-gallon waste/250-gallon freshwater stainless steel slide-in tank, and a 2001 3500 with a 400-gallon waste/150-gallon freshwater stainless steel slide-in tank. All have Jurop pumps.
For the septic installation work, equipment includes five excavators — four Bobcats (E35, E42, E50) and a small Kubota — a 14-foot dump trailer, a Bobcat skid-steer, and a Ford hydraulic tractor (“basically a glorified off-road forklift”). Equipment is hauled with Texas Pride and Texas Bragg tilt trailers. They use RIDGID and Goldak locating equipment.
For pumping septic tanks they’ve got a 2014 Peterbilt and a 2002 Freightliner built out by Longhorn Tank & Trailer with 3,700-gallon aluminum tanks and a 1998 Mack truck built out by Specialty B Sales with a 2,200-gallon steel tank, all with Jurop LC420 pumps.
About 90% of the portable restroom work is for construction projects but they also do a lot of weddings, provide units for Hobbs State Park and various lakes and parks, and service local events such as the Dogwood Festival; Fall Y’all Craft Fair; and Bikes, Blues and BBQ. They have a contract with the Flint Creek Power Plant to bring in about 60 units whenever the plant shuts down for maintenance.
And they provided units during the construction of the Crystal Bridges Museum of American Art sponsored by the Walton Family Foundation, a complex which includes galleries, classrooms, library, sculpture garden, restaurant and coffee bar.
WALMART WORK
Walmart is headquartered in Bentonville. Up until now, whenever they needed to expand their headquarters, they would do so by buying up vacant buildings around town, so they are quite spread out. But they are now three years into a seven-year project to bring everything together onto one campus. The project includes 12 office buildings on 350 acres and will house about 19,000 employees.
BBB currently has 91 restrooms, 23 hand-wash stations and 16 holding tanks on site, cleaned at least twice a week but often four or five times. One technician is dedicated to the project.
Work is done during the day. The technician uses one of the company’s vacuum trucks with a slide-in tank because the larger trucks don’t fit everywhere he needs to go. As a result, two or three times a day he makes a trip to a storage depot four miles away to dump loads and refill the water.
Currently the company has contracts with about eight different subcontractors. Units often get moved without the company’s knowledge, so they put identifying stickers on everything such that the technician knows which units are for which contractor for billing and accounting purposes.
COVERING ALL BASES
Jouvenaux uses five outside companies to assist him with marketing. There’s a person who manages the website, another who handles social media, a company that does things like ads on posters inside of restroom stalls and static ads on medical waiting room TV monitors.
Another company specializes in click funnels in the internet. “Basically it’s decision trees,” Jouvenaux explains. “The end result is it will decide which department a customer goes to. It will have already gathered all their information and built their customer file. All we need to do is check it and make sure it implements properly. It’s going to save us a ton of time on our admin but it’s also going to give a lot more turbo power to our marketing.”
The fifth company handles search engine optimization. “They have a program [Local Marketing Machine] that piggybacks on our software, which allows us to get reviews without our people having to ask for them,” Jouvenaux says. “Where our competitors might have 10 reviews, we’re north of 1,000. And we’re days away from implementing an AI portion of that that will help us with our scheduling.”
Jouvenaux meets with the team over lunch the first Wednesday of every month. “They all work together as if they were in the same company,” he says. “It’s a very well-tuned machine.”
The system is paying off. Jouvenaux says income has quadrupled in the last eight years due not only to their marketing efforts, but their dedicated crew and the company environment.
DOWN ON THE FARM
Over the years the company found it harder and harder to find places to dispose of waste. “It’s a national problem,” Jouvenaux says. “Municipalities are slowly cutting us off. Once our trucks are full, we’re out of business. So four or five years ago, our team started thinking about how we could do our own wastewater treatment.”
Their solution? They bought a farm. Then they bought a stainless steel In The Round Dewatering system featuring a skid-mounted cylinder (90 inches by 20 feet) that slowly turns loads of waste to remove water. The company now processes just over 3 million gallons a year through a combination of land application and dewatering, Jouvenaux says.
They set up three 22,000-gallon frac tank storage depots around their service area where technicians dump their loads through a screening process. The company uses two 4,700-gallon Peterbilts (2011, 2016) built out by Pik Rite with steel tanks and Jurop pumps for pumping out the tanks and hauling the contents to the farm for processing.
The wastewater first flows through a polymer injection area causing the solids to clump together and release water. Then it goes into the rotating dewatering cylinder. Water runs out into a 20,000-gallon underground tank and is used for irrigation.
“The solids are left to finish drying through the night, Jouvenaux says. “When we unload it, we’ve got a pile of what looks like black dirt. We’re exploring how we can turn that into biochar, which can be used as a soil amendment or heating fuel.
The Arkansas Department of Health monitors the operation. “They inspect the soil, send samples to a lab to make sure our nutrients are not out of whack and everything is in line,” Jouvenaux says. “We keep logs on how much we dump, how much we apply. Typically you’re not allowed to land-apply portable restroom waste, just septic, but because of the small relative volume and because we’re dewatering, we can do it.”
When neighboring farmers saw the company was getting more hay cuttings than they were, they wanted to participate in the program. The company is now in the process of obtaining a permit that would allow it to add farms.
FINDING SOLUTIONS
Jouvenaux says the creativity of his team is one of the things he loves most about the business. “Every day I enjoy coming to work because we’re always finding a better way to do things.” For example, early on, the company developed a method of transporting portable restrooms.
“You know how people say, ‘I should have patented that’? We created a model — a 16-pack and a 14-pack — where you slide the toilets in from the side, and there’s a rail down the middle of the trailer that holds the toe of the unit and you just put a cable around the back legs. Now, of course, they sell things like that at the WWETT Show.”
A recent innovation they’re currently finalizing is refashioning grit cleaning equipment from the mining and oil industries for use in the wastewater industry. “By doing that, on a normal septic truck, if it’s got a lot of trash in it and it’s what we would call a ‘dirty load,’ it might take an hour to run it through our current screen process to get the debris out,” Jouvenaux says. “With this new equipment, it’s 20 minutes.”
A great team that collaborates and works well together is key to innovation, Jouvenaux says. “We’re always looking for a better mousetrap,” It’s just fun. It’s like we’re kids with an Erector Set trying to figure out how to make a better machine.”